1.FIRST STEPS
Congratulations on your purchase of the ELITE model GBT 850 circular saw blades grinding machine.
Read this guide before you start.
The GBT 850 is an automatic grinding machine with double grinding wheel for the sides of the teeth, to repair or manufacture carbide-tipped circular saw blades from ø100 to ø850 mm.
Its operation is CNC with LCD screen. It allows a precise and fast grinding of the sides of the teeth.
You can view the product catalog at the following link: ELITE model GBT 850
This manual introduces you to the main functions of the grinder in order to avoid risks to your health or that may cause a breakdown or premature wear of the machine.
In case of any doubt, please contact us directly or one of our authorized distributors.
Informative Note: The use manual of the circular saw sharpener described therein may present some variations in use as our machinery is subject to possible construction modifications, depending on the incorporation of technological advances in our sharpening equipment.
2.SAFETY
2.1.Safety regulations
Carefully observe and apply the following safety rules, not respecting these rules may cause personal injury or damage to the machine itself.
The installation and maintenance of the machine described in this manual must be carried out only by operators who are familiar with its operation and have sufficient technical knowledge.
The ELITE sharpening machines of the GBT 850 model range have been designed for the grinding of the sides of circular saws with carbide teeth, excluding any other type of operation.
DANGER HIGH VOLTAGE
DANGER OF ACCIDENT
DANGER DUE TO SPARK PROJECTION
WEAR PROTECTIVE SHOES
DANGER FROM SHARP TOOLS
USE HEARING PROTECTORS
These warnings do not include all possible risks that improper use of the machine could cause. For this reason, the operator must proceed with prudence and observing the rules.
2.2.Use and storage of the instruction manual
This instruction manual must be read and understood by all personnel who come into contact with the machine.
This manual is for:
- Indicate the correct use of the machine according to the type of work to be carried out.
- Provide the necessary instructions for the transport, adjustment and maintenance of the machine.
- Facilitate the ordering of spare parts and information of risks.
Limits of use of the manual:
The machine is intended for professional use and therefore the experience of the operator is required and of vital importance.
Importance and conservation of the manual:
This manual must be considered part of the machine and must therefore be attached to it until the end of its use.
Additional information and clarifications:
The user, owner or maintenance person can contact the manufacturer to request any additional information on the use of the machine and possible modalities for maintenance and repair intervention.
Expiration of responsibility:
The manufacturer is considered exempt from any liability in the event of:
- Improper use of the machine
- Use of the machine by untrained persons
- Serious failures in scheduled maintenance
- Unauthorized interventions or modifications
- Use of non-original spare parts.
2.3.Declaration of conformity
The company hereby:
Elite Machines, SLU Joan Oró, 27
ES-08635 Sant Esteve Sesrovires
Declares that the product indicated below, based on its conception and construction, as well as the version put on the market by our company, complies with the mandatory basic health and safety requirements of the CE directive.
This declaration loses its validity in the event of unauthorized modifications to the product.
Product name: Elite model GBT 850
Product type: Circular saws sharpening machine
Serial No.: __
EC Directive Competences:
- EC Machinery Directive (2006/42/EC)
- European directive on electromagnetic compatibility (2014/30/EU)
- The protection purposes of the CE low voltage directive (2006/95/CE) were fulfilled according to annex I, nr. 1.5.1 of the machinery directive 2006/42/EC
The technical documentation was compiled by legal representative of the documentation:
Sergi Valls Gramunt
Joan Oró, 27
ES-08635 Sant Esteve Sesrovires
Date / manufacturer - Signature: __
Signatory data: Sergi Valls Gramunt, manager
3.TECHNICAL DATA
In the following information table, find the list of technical specifications of the sharpener described in this manual.
TECHNICAL DATA | GBT 850 |
---|---|
Saw blade diameter | From ø100 to ø850 mm. (4" to 33.5") |
Saw blade hole diameter | From ø10 mm. |
Sawtooth thickness | Up to 14mm. |
Saw body thickness | Up to 8mm. |
Tooth pitch | From 1 to 125 mm. |
Grinding wheel diameter | ø100 mm. (2 units) |
Grinding wheel hole diameter | ø20 mm. |
Automation | Using 4 CNC axes (X, Y1, Y2, A) |
Manual axles | B, Z |
Saw holding | By pneumatic clamp |
Motor wheel | 0.75 kW x 2 units |
Grinding wheel speed | Adjustable from 5000 to 9000 RPM |
Dimensions of the machine | 1650 x 1200 x 1900mm. |
Machine weight | 740 Kg. |
FLANK GRINDING | |
Grinding path | Up to 40 mm. (1,57") |
Rake angle | From -15º to +30º |
Radial cutting angle | From +5º to +6º |
Tangential cutting angle | From 0º to 8º |
REFRIGERATION EQUIPMENT | |
Tank capacity | 220 liters |
Coolant flow rate | Up to 40 liters/minute |
3.1 TECHNICAL REQUIREMENTS
A 6 bar air connection is required.
Connection voltage: 220/400V 2Ph 50/60Hz
Required connection power: 2.5 kW
3.2 EQUIPMENT INCLUDED
- Saw holder for small saw blade diameter of 100 to 210 mm.
- Saw holder for saw blades with a diameter of 210 to 850 mm.
- Centering ring: ø30 mm.
- Grinding wheel holder for sharpening wheels (two units).
- Feeding pawl of 3 mm.
- LED lamp lighting inside the work area
- Device for production of equal diameter saw blades
- Machine closed by enclosure.
- Prepared for connection to a machine filtration system or a centralized filtration system.
4.TRANSPORT
The ELITE GBT 850 is delivered packed in a wooden crate.
During all transport and transfer, the machine must be kept in its original vertical position, any variation in this position may lead to the loss of the guarantee.
Machine model | Dimensions (mm) | Weight (kg) |
---|---|---|
GBT 850 | 1920 x 1420 x 2020 mm. | 780 |
4.1.Instructions for unpacking and setting up
Take special care when lifting the load: The load may not be centered!
To lift or move the load, use a forklift with blades long enough to support the machine, taking into account the width and depth of the machine for the calculation of the weights to lift.
Once the packaging has been opened, remove the fixing stops from the feet of the machine
Before connecting the machine, remove any protection that the machine may have to protect the components during transport.
5.INSTALLATION
5.1.Machine placement
Before any work make sure that the machine is well aligned and does not oscillate at any of its ends, in which case it must be wedged to avoid movements. For its correct level it is necessary to use a leveling tool. This check must be carried out both longitudinally and transversally.
Poorly leveling the machine can cause unwanted vibrations and premature wear of the linear guides.
Remember: before connecting the machine, remove any protection that the machine may have to protect the components during transport.
WARNING: The machine must not be used under any circumstances by unqualified or unauthorized personnel.
5.2.Electrical connection
DANGER HIGH VOLTAGE!
The electrical connection of the machine must be carried out by qualified technical personnel only at the voltage indicated in the machine order / machine identification plate.
For any doubt about the voltage, consult the manufacturer before the connection.
Any claim for an incorrect connection will be out of warranty.
5.3.Main components of the machine
- Sliding door of the enclosure.
- Enclosure of the machine in the version with half cab.
- Control panel of the machine.
5.4.Control panel
- LCD screen
- Z axis up / grinding wheel up.
- X axis left / grinding wheel left.
- X axis right / grinding wheel right.
- Encoder to navigate through screen menus.
- Z axis down / grinding wheel down.
- Indexing pawl movement up/down.
- Clamping open/close.
- LED cabin light switch ON/OFF.
- Cooling pump ON/OFF.
- START button.
- STOP button.
- Emergency stop.
6.STARTING UP
In this section we show you to operate the ELITE GBT 850 in order to work.
NOTE: The data that appears in the different images are by way of example, each type of tool has its recommended data and a skilled operator must know them.
Emergency stop
It's the round red button. In the event that there is a failure in use or a dangerous situation is being created, it allows the immediately disconnection of the machine.
Should not be used unless strictly necessary.
Once used, to use the machine again, you must pull it to return to the initial position, additional referencing and setting up must be needed.
WARNING: Under no circumstances should this control be modified or manipulated, this automatically puts the operator and people around him in danger of serious injury.
Sharpening operation
To start the sharpening process, you must first make sure that the emergency stop button is not activated.
DANGER: never manipulate the buttons on the control panel while changing the abrasive wheel: danger of very serious injuries. It is highly recommended to switch off and disconnect from power mains the machine when working inside the machine.
WARNING: before start to rotate the grinding wheel make sure that it is well attached to the wheel holder where it is located and that NOBODY is manipulating in the area where it rotates. UNDER NO CIRCUMSTANCES SHOULD THE WHEEL BE STARTED WHILE SOMEONE IS HANDLING IT.
6.1.Machine power on and axis homing
Turn the machine on with the main switch in the ON position, deactivate the emergency stop in case it is active.
The machine's screen turns on and the green light of the indicator lamp also lights up.
In order to center the machine, first make sure to close the cab. Follow the instructions that appear on the control panel menu screen. Press the start button (START) and verify that an indication appears on the screen indicating that the axes are going to be referenced.
When you press the start button again, the display will alert you that the machine is about to reference the trigger.
Next, the screen will ask you to center the abrasive stones with the gauge. To do this, open the cabin and introduce a saw whose body thickness must have been previously measured and these parameters entered in the process values on the machine so that you know the width of the saw.
Place the saw in the chuck, clamp it, and on the menu screen, press the jaw lock button.
Next, you must bring the abrasive stones (2) closer so that they rub against the body of the saw. Using the Y1 or Y2 axis movement selector, you must select which of the two stones should be moved. Turning the selector to the left, the program will move the outer stone to proceed to center it. Once the outer stone is centered, proceed to turn it clockwise to move only the inner stone. Once this step is done, place the selector back in the center.
IMPORTANT: during the automatic program, the selector should not be changed under any circumstances. Otherwise, the abrasive stones would be out of center and this operation would have to be repeated again.
After completing these steps, the machine has finished referencing and is ready to work. The different work programs will appear on the menu screen.

6.2.Changing the grinding wheel
Necessary tools: allen wrench No. 4.
With the machine switched off, remove the four allen screws from the front of the grinding wheel. Hold the wheel and wheel holder ring throughout so that it does not fall.
Now insert the new grinding wheel.
Reposition the locating ring in the correct position so that the locating pin passes through the locating ring.
Replace the allen bolt and tighten.

6.3.Changing the saw holder
The ELITE model GBT 850 sharpening machine comes equipped with two (2) saw blade supports. One up to ø850 mm and another support for small saw blades <ø200 mm..
To exchange the supports, remove the two (2) screws and save them. Now we have the support outside. It is important to make sure that when the support comes out, the centering pin remains in its position. When the 10 mm centering pin wears out due to using, it will be necessary to be exchanged for a new one.
Next, place the other saw blade support, and make sure to fix it again. Now, the centering pin itself limits the diameter that we can put on the saw blade.
The mounting of the saw blade is the same as with the other support: use a centering ring and now we can mount the saw blade to be sharpened. It is ready to work.

6.4.Adjustment of the indexing feed cam according to the diameter of the circular saw
Depending on the diameter of the blade, the indexing feed cam will need to be adjusted in order for the indexing pawl to advance the teeth of the saw.
NOTE: To adjust the indexing feed cam the indexing feed pawl must be in its lower position. Otherwise the force of the spring will move the indexing pin to the lowest position and we will lose the current position.
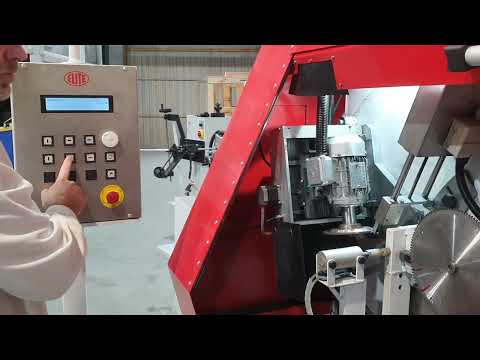
7.WORK OPERATION
7.1.Program editting
The grinding machine has several programs where the work values can be edited.
On the menu screen, confirm the Programs option by clicking on the OK option to enter the first program.
Program number one is made up of six screens. In the first, edit the values concerning to the number of teeth, the final width that the tooth is required to have, and the thickness of the body of the saw to be ground.
These values will allow the machine to center the disc tooth.
On the second screen, you will need to enter the amount of roughing required per pass; how much roughing is desired for each pass of the stone and the working speed of the Y axis (load of sharpening of the stone). Next, you must edit the value for the finishing passes, that is, the amount of material that needs to be removed for each finishing pass, where the first value indicated corresponds to the total amount and the second; to the amount per pass. The last of the values of this same line allows you to edit the speed at which the finishing is going to be carried out.
And finally, it can be edited if the lapping passes are required: No-load passes where only the tooth is polished and the feed rate is set.
Normally, the speed ratio of these 3 processes described above is as follows:
ROUGHING>FINISHING>LAPPING
The roughing speed being the fastest of the three and the lapping speed being the slowest. In this way, the best quality is achieved in the tooth.
On the next screen, you will enter the sharpening path, which generally corresponds to the length of the tooth plus 1-2mm so that the stone can come out.
On the second line, you can edit the tooth pitch and where the load is applied with the grinding stone. These 3 options can be configured: at the beginning of the tooth (in front), at the end of the tooth (behind) or in both routes.
The following parameters that the menu screen will allow you to edit are: the speed of the indexing finger and the speed at which the grinding wheel must rotate. Usually, it is 9000 rpm for ø100 mm grinding wheels.
Finally, you must indicate in the program the angle that the teeth has; its trapezoid angle.
For information purposes, the program will indicate the recorded cutting angle, this data is only for informative purposes and you can store it here for further data recovery. The angle is selected manually on the grinder using the external indicator on the lever.
In case of conformity of the entered values, you must proceed to save the program and press the START button to transmit the data. Be sure to close the enclosure door, otherwise as a security measure the program will not start. Once closed, press the start button, now the grinding wheels will start to rotate. You will notice that the menu screen indicates that you should touch the grinding wheel with the tooth. Meanwhile, the program will be indicating the position of each of the axes. This function will allow placing the axes in the same position in the event that it is required to grind circular saws of identical sizes.
Finally, on the approximation process you can set the speed of the axis to move it fast or slow for fine tuning. This is done by clicking button 4 (menu browser), the LCD screen will indicate the selected speed.
By pressing the START button again, the machine will proceed to run the automatic process introduced in the programed values of the LCD screen.
Programming for grinding the ELITE GBT 850
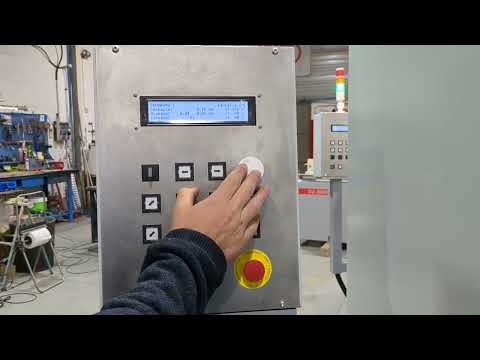
7.2.Flank grinding
ELITE GBT 850 flank grinding
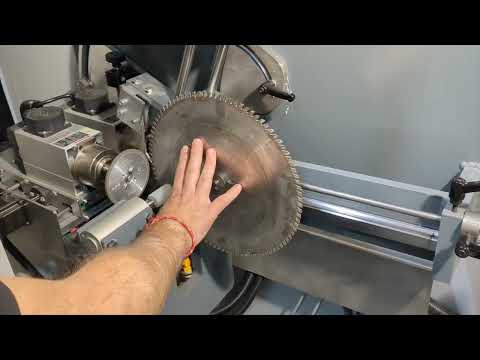
8.MAINTENANCE
8.1.Preventive maintenance
The maintenance of the ELITE model GBT 850 grinding machines is very simple but at the same time important.
It consists of the following:
- Cleaning and greasing the polished parts, in case the machine is not used for several days, to prevent oxidation.
- Check the level of coolant in the coolant tank. You can use to refill the coolant the ELITE SintoCut PRO MIX. The coolant should be mixed with water between 2 and 8%. Being below it can lead to oxidation of mechanical parts and if the level is higher it can be toxic. - Monthly.
- The sludge and dirty that is deposited both in the work area and in the coolant tank must be emptied - Weekly.
- Keeping the machine clean and in good condition will allow for optimal long-term use.
Use the equipment only in dry environments. The temperature must be between 5 and 40ºC. A relative humidity greater than 90%, as well as a saline environment, would cause premature corrosion of the machine.
To lubricate the pneumatic circuit we recommend using Esso Spinesso oil
9.ACCESSORIES AND CONSUMABLES
9.1.Grinding wheels
For the grinding wheel use the ref. nr. 2310-A. 1A1 D107 C75 ø100x4x5x10xø20 mm.
9.2.Coolant agents
We recommend to use ELITE SintoCut PRO MIX or equivalent to mix with water emulsion. If you prefer to grind with oil, you can use our SintoCut PRO MD. Both coolant are available in 20 liters can or 200 liters barrel.
9.3.Equipment
Additional equipment of the machine.
9.3.1.Filtering systems
Machine could be equipped with one of the following ELITE filtering systems. If your machine already has one of this systems and you need information or help, please refer to the manual of the filtering system.
9.3.1.1.FILTRAmaq UNO
Filtering system integrated in the machine to save space.
9.3.1.2.FILTRAmaq SOLO
Independent filtering system for one machine.
9.3.1.3.FILTRAmaq PRO
Centralized filtering system for up to 5 machines.
10.WARRANTY
All our machines are tested before being shipped. However, there can always be defects that are not observable at first sight.
Our machines are guaranteed against manufacturing or material defects under normal use and maintenance conditions.
The period of this guarantee is 12 months from the date of purchase and consists of the replacement of defective material.
The guarantee will be automatically canceled in the event of a modification outside our company. Or in manifest cases of misuse of the machine.
The guarantee does not include parts subject to normal wear due to use such as skids, lubrication cartridge, abrasives, etc.
11.DOWNLOAD MANUAL
User Manual GBT 850 DUO - EN.pdf
12.FAQ
Question nr1
Answer no. 1