1. GETTING STARTED
Congratulations on your purchase of the ELITE 70 universal tool sharpener.
Please read this guide before you begin.
The ELITE 70 is our highly accurate and robust universal tool sharpener, designed for the toughest jobs, as it can load up to 200 kg on the work table, achieving micron precision for the most demanding sharpening or grinding of your cutting tools.
You can view the product catalog at the following link: ELITE 70
This manual introduces you to the main functions of the sharpener in order to avoid risks to your health or that may cause a breakdown or premature wear of the machine.
If you have any questions, please contact us directly or one of our authorized distributors.
Informative Note: The user manual for the universal tool sharpener described in it may present some variations in use as our machine is subject to possible construction modifications, depending on the incorporation of technological advances in our sharpening equipment.
2.SAFETY
2.1.Safety regulations
Please observe and apply the following safety regulations carefully. Failure to comply with these regulations may result in personal injury or damage to the machine itself.
The installation and maintenance of the machine described in this manual must only be carried out by operators who are familiar with its operation and have sufficient technical knowledge.
The ELITE 70 sharpening machine has been designed for sharpening milling cutters and cutting tools, excluding any other type of operation.
DANGER HIGH VOLTAGE
DANGER OF ACCIDENT
DANGER DUE TO SPARK PROJECTION
WEAR PROTECTIVE SHOES
DANGER FROM SHARP TOOLS
USE HEARING PROTECTORS
These warnings do not include all possible risks that improper use of the machine could cause. For this reason, the operator must proceed with prudence and observing the rules.
2.2.Use and storage of the instruction manual
This instruction manual must be read and understood by all personnel who come into contact with the machine.
This manual is for:
- Indicate the correct use of the machine according to the type of work to be carried out.
- Provide the necessary instructions for the transport, adjustment and maintenance of the machine.
- Facilitate the ordering of spare parts and information on risks.
Limits of use of the manual:
The machine is intended for professional use and therefore the experience of the operator is required and of vital importance.
Importance and conservation of the manual:
This manual must be considered part of the machine and must therefore be attached to it until the end of its use.
Additional information and clarifications:
The user, owner or maintenance person can contact the manufacturer to request any additional information on the use of the machine and possible modalities for maintenance and repair intervention.
Expiration of responsibility:
The manufacturer is considered exempt from any liability in the event of:
- Improper use of the machine
- Use of the machine by untrained persons
- Serious failures in scheduled maintenance
- Unauthorized interventions or modifications
- Use of non-original spare parts.
2.3.Declaration of conformity
The company hereby:
Elite Machines, SLU Joan Oró, 27
ES-08635 Sant Esteve Sesrovires
declares that the product indicated below, based on its conception and construction, as well as the version put on the market by our company, complies with the mandatory basic health and safety requirements of the CE directive.
This declaration loses its validity in the event of unauthorized modifications to the product.
Product name: ELITE 70
Product type: Universal tools sharpening machine
Serial No.: __
EC Directive Competences:
- EC Machinery Directive (2006/42/EC)
- European directive on electromagnetic compatibility (2014/30/EU)
- The protection purposes of the CE low voltage directive (2006/95/CE) were fulfilled according to annex I, nr. 1.5.1 of the machinery directive 2006/42/EC
The technical documentation was compiled by Legal representative of the documentation:
Sergi Valls Gramunt
Joan Oró, 27
ES-08635 Sant Esteve Sesrovires
Date / manufacturer - Signature: __
Signatory data: Sergi Valls Gramunt, manager
3.TECHNICAL DATA
In the following information table, find the list of technical specifications of the machine described in this manual.
TECHNICAL DATA | ELITE 70 |
---|---|
Grinding wheel motor | From 3000 to 9000 RPM and 2 HP (Optional up to 18000 RPM) |
Grinding wheel diameter | Up to ø150 mm. |
Work table dimensions | 870 x 160 mm adjustable from +90º to -90º |
Useful travel of the X axis | 550 mm. |
Useful travel of the Y axis | 200 mm. |
Useful travel of the Z axis | 400 mm. |
Vertical spindle rotation | 360º |
Horizontal spindle rotation | 180º |
Maximum weight on the table | 200 Kg. |
AVAILABLE VERSIONS | ||
---|---|---|
Model | Packaging size | Weight |
CNC version | 2340 x 1970 x 1920 mm. | 1400 Kg. |
Manual version | 2340 x 1970 x 1920 mm. | 1075 Kg. |
4. TRANSPORT
The ELITE 70 is delivered packed in a wooden crate.
During all transport and transfer the machine must be kept in its original vertical position, any variation in this position may result in the loss of the warranty.
Machine model | Dimensions (mm) | Weight (kg) |
---|---|---|
CNC version | 2340 x 1970 x 1920 | 1400 |
Manual version | 2340 x 1970 x 1920 | 1075 |
4.1. Instructions for unpacking and setting up
The ELITE 70 model sharpening machine leaves our facilities properly prepared so that its mechanisms do not suffer any damage during transport. For this reason, and to put it in working order, it requires some operations detailed below:
The machine must be moved to its location without removing any of the packaging that has been provided for its transport.
When designating the location where the machine will be located, it must be taken into account that the floor is compact and free of vibrations.
Once it has been placed in the room, you can proceed to carefully remove the packaging. Remove the fixing stops from the feet of the machine
Use slings that can easily support the weight of the machine to move the machine. On the front and back of the machine you will find holes for attaching slings.
Hooks on the front of the machine. Rear hooks.
4.1.1. Machine with manual table movement version
If the machine is configured with manual table movement, it will be properly blocked as follows:
The machine is shipped with the table blocked by the stops in figure No. 1.
To unlock the table, loosen the hexagonal screw with a No. 19 wrench and secure it in the part where you want the travel. NEVER REMOVE THE STOPS! THEY MUST ALWAYS BE FIXED. The limit of the fixation is indicated on the limit screws in figure No. 2.
NEVER REMOVE THE CENTRAL STOP (Figure No. 3) as this would eliminate the limit of travel of the table with respect to the stops No. 1.
Detail of the left stop at the limit of travel.
FOR SAFETY: DO NOT UNLOCK THE TABLE UNTIL THE MACHINE HAS BEEN TRANSPORTED TO ITS FINAL WORKING POSITION AND ONCE IT HAS BEEN LEVELED.
5. INSTALLATION
5.1. Positioning the machine
Before any work, we must ensure that the machine is properly aligned and does not oscillate at any of its ends. In this case, it must be supported to prevent movement. To ensure that it is correctly level, a spirit level must be used. This check must be carried out both longitudinally and transversely.
Level the machine using the foot screws provided. Poor leveling of the machine can cause unwanted vibrations and premature wear of the linear guides.
Unlock the various movements and clean the protective liquid with which some parts are coated.
ATTENTION: The machine must not be used under any circumstances by unqualified or unauthorized personnel.
5.2. Electrical connection
DANGER HIGH VOLTAGE!
Remember: before connecting the machine, remove any protection that the machine may have to protect the components during transport.
The electrical connection of the machine must be carried out by qualified technical personnel only at the voltage indicated on the machine order.
Check that the electrical voltage indicated on the machine corresponds to that of the electrical network.
If you have any doubts about the voltage, consult the manufacturer before connecting it.
Any claim for incorrect connection will be void of warranty.
5.3.Main components of the machine - Manual version
A. Vertical movement handwheel
B. Grinding wheel guard
C. Degree adjustment in the vertical plane of the vertical column.
D. Fixing for the rotation of the table in the horizontal plane.
E. Adjustment stops for the longitudinal travel of the table.
F. Longitudinal movement handwheel.
G. MPG encoder for raising/lowering the vertical movement (Optional).
H. Emergency stop.
I. Selection of the direction of rotation of the grinding wheel
J. Regulation of the speed of rotation of the grinding wheel.
K. Machine feet (4 units)
L. Accessory storage door (There is one more unit on the left side of the machine).
M. Cooling system activation button (Optional).
N. Emergency stop reset button.
O. Hooks for loading/unloading the machine using slings (4 units).
P. Transverse movement handwheel.
5.3.1.Main machine components - CNC version
- Control panel
- Machine status indicator light
- Magnifying glass with LED lighting (Optional)
- Vertical movement column
- Vertical movement handwheel for grinding wheel
- Grinding wheel motor
- Lighting lamp
- Coolant outlet (Optional)
- Work table
- Coolant collection tray (Optional)
- Electrical panel
- Machine fixing feet (4 pcs)
- Front cover for tool storage
- Hooks for machine transport (4 pcs)
5.4.Control panel - Manual version
- Emergency stop
- Selection of the grinding wheel rotation direction
- Grinding wheel rotation speed selector
- Cooling system activation button (Optional).
- Machine reset.
5.4.1. Control panel - CNC version
- Machine power on indicator light
- Machine in automatic mode indicator light
- LCD screen
- Screen menu selector
- Lighting lamp on/off
- Cooling system on/off (Optional)
- Emergency stop
- Axis speed selector.
- Automatic cycle stop button
- Automatic cycle start button
- Manual axis movement selector (Depending on the machine configuration, there may be 1 to 4 axes).
6.START-UP
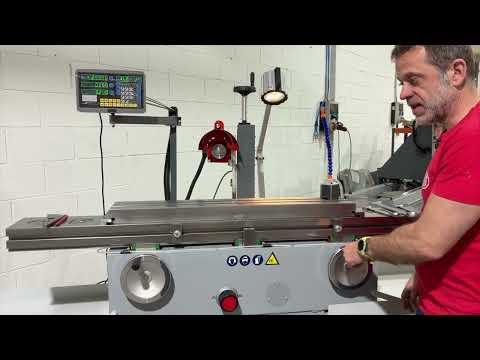
6.1.Power on the machine
In this section we show you how the buttons on the control panel of the ELITE 70 work.
NOTE: The data that appears in the different images are by way of example, each type of tool has its recommended data and the sharpening professional must know them.
Emergency stop
It's the red button at the bottom right, in the penultimate row of buttons. In the event that there is a failure in use or a dangerous situation is being created, it allows the automatic disconnection of the machine.
Should not be used unless strictly necessary.
Once used, to use the machine again, you must pull it to return to the initial position.
WARNING: Under no circumstances should this control be modified or manipulated, this automatically puts the operator and people around him in danger of serious injury.
Sharpening Operation
To start the sharpening process, you must first make sure that the emergency stop button is not activated.
The two types of modes it can operate in are STOP MODE and START MODE.
DANGER: never manipulate the buttons on the control panel while changing the abrasive wheel: danger of very serious injuries.
WARNING: before starting the grinding wheel we must make sure that it is well attached to the axis where it is located and that NOBODY is manipulating in the area where it rotates. UNDER NO CIRCUMSTANCES SHOULD THE WHEEL BE STARTED WHILE SOMEONE IS HANDLING IT.

6.2.Power on and referencing
On the machine with CNC control panel, after the machine is turned on you will be asked to reference the automated axes.
To do this, check that the machine can move freely without colliding with any object or person, then press the STRAT button to confirm the referencing process.
When the machine finishes the process, it will remain stationary in the final position of the referenced axes, and will be ready for normal working operation.
Referencing of the axes and manual movement.

6.3.Safety
A grinding wheel guard must always be used when using the machine. Two grinding wheel holders are included, depending on the diameter of the grinding wheel to be used (Figures No. 1 and 2). To do this, remove the grinding wheel holder that is not going to be used by loosening the screw Figure No. 5.
To use the grinding wheel holder in Figure No. 2, the height of the clamping bar (Figure No. 3) must be in the lowest position (Figure No. 4). And to use the large grinding wheel holder, it must be in the highest position.
7.SHARPENING OPERATION
7.1. Grinding wheel holder and vertical movement
Direct drive precision grinding wheel motor with variable speed from 3000 to 9000 RPM and 1.5 HP. (Optionally available up to 18,000 RPM).
The vertical movement of the grinding wheel is carried out by the upper handwheel in the case of the manual machine, or by means of an MPG encoder located on the front of the machine in the case of motorized vertical movement.
In the case of a CNC version of the grinding machine and this axis is automated, the movement will be carried out from the control panel with its corresponding arrows
7.2.Rotation movement of the grinding wheel head
The grinding wheel head can rotate 180º with respect to its vertical axis and 360º with respect to the horizontal axis.
7.3.Frontal movement
This can be activated by the second handwheel on the left with respect to the front of the machine, its operation is manual.
In case the sharpening machine is in CNC version and this axis is automated, the movement will be done from the control panel with its corresponding arrows
7.4. Longitudinal movement
This is done by means of the handwheels located on the left and right of the front of the machine, as well as at the back for operators who wish to work at the back of the machine.
If you wish to set or limit the travel of the work table in a longitudinal direction, there are adjustment or fixing stops located on both sides of the front of the table.
If the sharpening machine is a CNC version and this axis is automated or the option chosen has motorized table movement, the movement will be done from the control panel with its corresponding arrows.
7.5. Optional equipment
The Elite 70 sharpening machine can be optionally equipped with a cooling unit consisting of:
- 15 litre tank.
- Pump
- Tubes and nozzle with regulating tap.
For cooling we recommend using Sintocut PRO MIX cooling fluid in a proportion of 3-5 %.
It can also be additionally equipped with a chip extraction system resulting from sharpening.
7.6. Settings
7.6.1. Head travel
The sharpening head is fixed to the vertical column of the machine and can be rotated in the horizontal and vertical planes.
The handwheel on the upper column will move the grinding wheel up or down. Each turn of the handwheel represents a movement of 4 mm.
The sharpening head can be tilted in the horizontal and/or vertical plane by loosening two bolts.
ATTENTION: TAKE PARTICULAR CARE TO HOLD THE SHARPENING HEAD WHEN IT MOVES IN THE VERTICAL PLANE!!!
The safety cover can also be rotated 360° by the fixing screw on the top of the cover.
7.6.2.Work table
There are two 14mm wide T-slots on the work table, in which any type of accessory can be fixed in a suitable position.
The movement of the table is carried out by means of the front handwheels.
The travel of the work table can be adjusted by means of the two locks located on the front of the sharpening table.
7.6.3. Sliding upper table
The upper table can be rotated 360°. To do this, you must loosen the two pins located on the left and right of the table as well as the central allen screw.
7.7.Operation
The type of application or work that can be performed with the ELITE 70 universal sharpening machine will vary depending on the accessories or additional equipment with which the machine has been configured at the time of ordering and depending on the work to be performed by the customer.
The ELITE 70 sharpening machine can perform the following jobs, always depending on the accessories with which it is configured. These accessories constitute additional equipment that can be added to the base machine. Here are some examples of applications:
- Sharpening of cylindrical cutters
- Sharpening of single-angle cutters
- Sharpening of T-slot cutters
- Sharpening of three-cut cutters
- Sharpening of end mills
- Sharpening of blades
- Sharpening of cutting tools
- Sharpening of threading taps
- Sharpening of drills
- Sharpening of lathe tools
- Sharpening of reamers
- Sharpening of hob cutters for gears
- Sharpening of pinion cutters
- Sharpening of tools between points (Trompos, etc.)
- Surface grinding
8. MAINTENANCE
8.1. Preventive maintenance
CAUTION: Do not clean or perform maintenance on the machine while it is connected to the power supply:
It may cause damage to the machine and to the person. Switch off the machine and disconnect it from the power supply before carrying out any maintenance or cleaning work
- The machine is low maintenance and contains only a few parts, which must be maintained.
- Any fault or defect that may affect the safety of the machine must be eliminated immediately.
- Repair activities may only be carried out by qualified personnel
- Thorough cleaning ensures a long life for the machine and is a safety requirement.
- The use of solvents, aggressive chemicals or abrasive cleaning products may damage the machine casing. For cleaning use only mild detergents.
- Apply a light coat of anti-corrosion agent (e.g. WD40) to unpainted surfaces of the machine.
- After each work shift, the machine and all its parts are thoroughly cleaned of dust and chips with a vacuum cleaner. Do not use compressed air to clean it, as it embeds the particles inside the guides and bearings.
- Check regularly that all warnings and safety instructions are available on the machine and perfectly legible.
- Before each use, check the condition of the safety devices.
- Use the equipment only in dry environments. The temperature must be between 5 and 40ºC. Relative humidity greater than 90%, as well as a saline environment, would cause premature corrosion of the machine.
8.1.1. Lubricating the machine
The machine is equipped with a manual lubrication system. You should operate it once a week, ensuring that the oil reaches all the parts you lubricate. To do this, check that the semi-transparent tubes are full of oil.
ATTENTION: Repair work may only be carried out by qualified personnel.
Lack of maintenance will void the warranty and warranty claims
9.ACCESSORIES AND CONSUMABLES
9.1.Abrasive wheels
9.1.1.Sharpening cutters
For the sharpening of strawberries we recommend the following reference: 2141-A. 4A2. ø150x4x2x12xø20 mm.
For sharpening carbide burs with a narrow pitch we recommend the following reference: 2150-A. D76 C125. ø150x13x2.9x13xø32 mm.
9.2.Cooling agents
9.2.1.Work only with steel and HSS
We recommend using ELITE SintoCut MIX or equivalent when working only with steel.
9.2.2.Working with steel and carbide
If the machine is to work with steel and also with tungsten carbide, then it is better to work with SintoCut PRO MIX or equivalent, which is a better choice for working with carbide.
9.3.Additional accessories
9.3.Equipment
9.3.1.Filtering systems
The machine could be equipped with one of the following ELITE filtering systems. If your machine already has one of these systems and you need information or assistance, please refer to the filtering system manual.
9.3.1.1.FILTRAmaq UNO
Self-contained equipment for the filtration of grinding/sharpening liquids, up to 2 µm. It is ready to be installed inside the tank of ELITE machines.
9.3.1.2.FILTRAmaq SOLO
Independent filtering system for one machine.
9.3.1.2.FILTRAmaq PRO
Centralized filtration system for the connection of up to 5 machines.
10. WARRANTY
All our machines are tested before being shipped. However, there can always be defects that are not observable with the naked eye.
Our machines are guaranteed against manufacturing or material defects under normal use and maintenance conditions.
The period of this guarantee is 12 months from the date of purchase and consists of the replacement of defective material.
The guarantee will be automatically canceled in the event of a modification outside our company. Or in manifest cases of misuse of the machine.
The guarantee does not include parts subject to normal wear due to use such as skids, lubrication cartridge, abrasives, etc.
12.DOWNLOAD MANUAL
13.FAQ
Question nr1
Answer no. 1